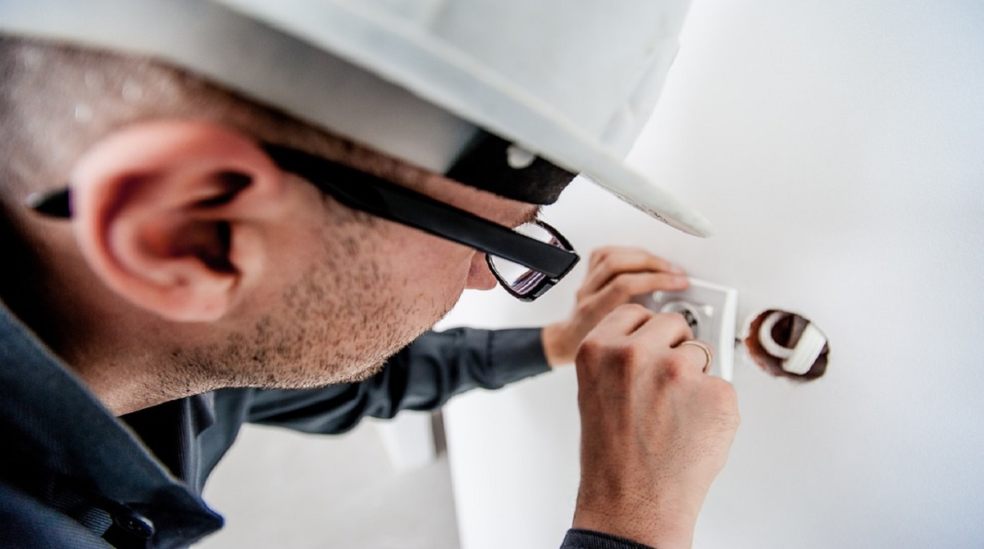
Electrical Preventive Maintenance Checklist for Facilities
When managing electrical systems in your facilities, staying proactive is key to avoiding costly downtime and safety hazards.
By adhering to a structured preventive maintenance checklist, you can considerably reduce the likelihood of unexpected failures and guarantee the smooth operation of your equipment.
But what specific steps should you take to create an effective checklist that covers all essential aspects of electrical maintenance?
Let's explore the fundamental components that will help you safeguard the Carda Electrics facility's electrical infrastructure and maintain peak performance levels.
Key Takeaways
- Regular visual inspections for wear and damage detection.
- Performance testing under load conditions.
- Checking for loose connections, corrosion, and overheating.
- Testing tools like multimeters and thermal imaging.
- Proactive maintenance for longevity and safety.
Inspection and Testing Procedures
Regularly conducting thorough inspection and testing procedures is essential for maintaining the ideal functionality and safety of electrical equipment.
Inspecting electrical connections, wiring, and components for signs of wear or damage guarantees early detection of potential issues. Testing equipment performance under load conditions helps verify operational efficiency and reliability.
By checking for loose connections, corrosion, or overheating, you can prevent unexpected failures and hazardous situations. Utilizing testing tools like multimeters and thermal imaging cameras enhances the accuracy of assessments.
Regular inspections and testing not only prolong the lifespan of equipment but also contribute to a safer working environment. Stay proactive in your approach to maintenance to guarantee the continued peak performance of your electrical assets.
Equipment Condition Assessment
Conducting thorough assessments of equipment conditions is vital for guaranteeing ideal functionality and safety in electrical systems. To keep your systems running smoothly and prevent unexpected failures, consider the following key points:
Regular visual inspections are essential to identify any visible signs of wear or damage.
Testing equipment regularly helps detect issues early on and guarantees peak performance.
Monitoring equipment age and usage patterns aids in determining maintenance frequency and requirements.
Keeping detailed records of maintenance history allows for better tracking of equipment conditions over time.
Utilizing manufacturer recommendations as a guide for maintenance practices guarantees adherence to best practices and standards.
Asset Prioritization and Scheduling
Prioritizing assets and scheduling maintenance tasks are essential steps in guaranteeing the ideal performance and longevity of electrical equipment.
By categorizing equipment based on criticality and usage patterns, you can determine which assets require immediate attention. Start by creating a priority list that considers factors like equipment age, maintenance history, and impact on operations.
Once assets are prioritized, develop a maintenance schedule that guarantees regular upkeep and inspections. Distribute maintenance tasks evenly throughout the year to prevent overload and guarantee consistent monitoring.
Technology Integration for Maintenance
Integrating technology into maintenance processes streamlines operations and enhances efficiency in managing electrical assets. Here are five key ways technology can revolutionize your maintenance practices:
- Remote Monitoring: Utilize IoT devices to remotely monitor equipment health and performance.
- Predictive Maintenance Tools: Implement software that predicts maintenance needs based on data analytics.
- Mobile Applications: Use mobile apps for on-the-go access to maintenance checklists and work orders.
- Asset Management Systems: Employ digital platforms to track asset lifecycles and maintenance histories.
- Augmented Reality: Explore AR applications for troubleshooting and guiding maintenance tasks with visual aids.
Data-Driven Decision Making
Data-driven decision-making empowers maintenance teams to optimize resource allocation and enhance operational efficiency through informed insights derived from data analysis.
By leveraging data, you can identify trends, predict equipment failures, and allocate resources more effectively.
Analyzing maintenance records and equipment performance data enables you to schedule maintenance tasks strategically, minimizing downtime and maximizing equipment lifespan.
Utilizing maintenance software for data collection and analysis streamlines the decision-making process, ensuring that actions are based on factual information rather than assumptions.
With data at your disposal, you can make proactive decisions, prioritize critical maintenance tasks, and allocate resources efficiently, ultimately leading to improved operational performance and reduced costs in the long run.
Risk Assessment and Resource Allocation
Performing a thorough risk assessment is essential for effectively allocating resources in electrical preventive maintenance planning.
To guarantee your maintenance efforts are targeted and efficient, consider the following:
- Identify critical electrical assets that pose the highest risk if they fail.
- Evaluate the likelihood and potential impact of failures on operations.
- Prioritize maintenance tasks based on the level of risk associated with each asset.
- Allocate resources such as time, manpower, and budget according to the identified risks.
- Regularly review and update risk assessments to adapt to changing conditions and priorities.
Employee Training and Safety Measures
To guarantee the effectiveness of your electrical preventive maintenance efforts, prioritize employee training and implement robust safety measures.
Adequate training ensures that your staff can identify potential electrical hazards, perform maintenance tasks correctly, and respond to emergencies promptly. Conduct regular safety training sessions to educate employees on best practices, safety protocols, and the proper use of personal protective equipment.
Emphasize the importance of following safety guidelines and reporting any issues or concerns promptly. Encourage a safety-first culture in your workplace to reduce the risk of accidents and injuries.
Frequently Asked Questions
How Can I Calculate the Cost Savings From Implementing an Electrical Preventive Maintenance Plan?
To calculate cost savings from implementing an electrical preventive maintenance plan, assess reduced repair expenses, increased equipment longevity, and enhanced operational efficiency. Regular upkeep minimizes unexpected failures, optimizing equipment functionality and lowering ownership costs.
What Are the Common Challenges Faced When Transitioning From Reactive to Preventive Maintenance?
When shifting from reactive to preventive maintenance, you'll encounter challenges like moving from fixing issues post-emergence to proactive identification, adjusting resource allocation, and implementing new technology. Proper planning and training can ease this shift.
Can You Provide Examples of Key Performance Indicators (Kpis) Used to Measure the Success of Preventive Maintenance?
Track KPIs like equipment uptime, mean time between failures, and maintenance costs to measure preventive maintenance success. These metrics gauge efficiency, reliability, and cost-effectiveness. Please utilize them for continuous improvement and proactive equipment upkeep.
What Are the Best Practices for Integrating New Electrical Equipment Into an Existing Preventive Maintenance Plan?
When integrating new electrical equipment into your preventive maintenance plan, prioritize creating an asset list and incorporating the new assets based on criticality. Regularly assess their condition and adjust maintenance schedules accordingly for peak efficiency.
How Can Facilities Ensure Compliance With Regulatory Standards and Guidelines During Preventive Maintenance Activities?
Guarantee compliance by regularly reviewing regulatory standards, updating procedures accordingly, and training staff on requirements. Utilize technology for accurate record-keeping and audits. Proactive measures prevent violations, guaranteeing a safe and compliant work environment.
Conclusion
In summary, by consistently following an electrical preventive maintenance checklist for facilities, provided by Carda Electrics, you can guarantee the safety and efficiency of your operations.
Regular inspections, testing, and documentation are key to detecting issues early and avoiding costly breakdowns.
Prioritizing assets, integrating technology, and training employees all play an essential role in maintaining a secure working environment.
Stay proactive and stay safe by implementing an extensive preventive maintenance program for your facility with Carda Electrics.